How to approach the power quality problem
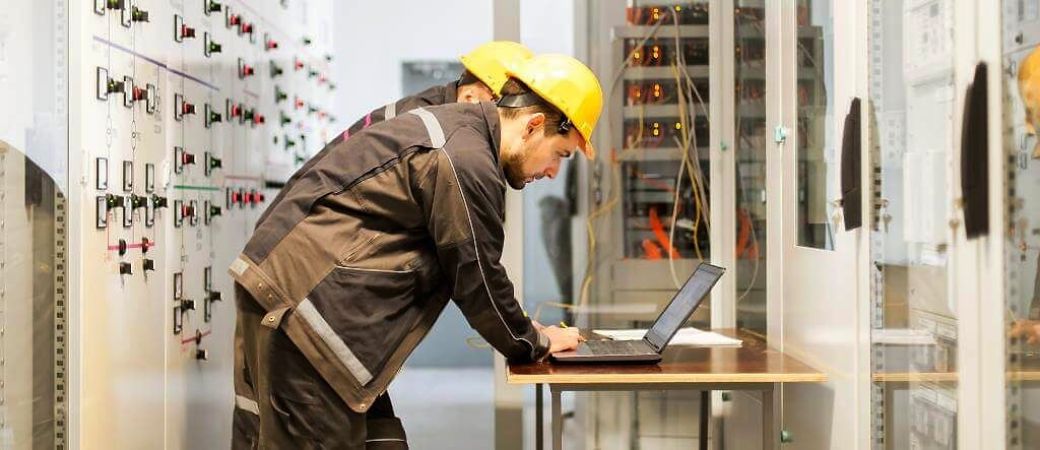
If you belong in the continuously growing number of industrial units which apply automation and control systems in the production process, then you are certainly concerned – or you should be concerned – about the issue of Power Quality.
In recent years, more and more industrial units are implementing automation and control systems in an effort to ensure uninterrupted and efficient production.
How power disorders are created?
However, the increasing use of automation and control systems creates the problem of poor Power Quality. The more automation is used, the more intense the problem of poor power quality can become.
According to statistics, about 80% of power quality disorders are generated internally by the downstream system – usually by non-linear loads such as inverters, transformers, welds, motors, robots, and other similar types of equipment.
All the above creates the problem of harmonics in the installation of high power loads (for example large motors), which can cause power quality disorders.
The remaining 20% of disturbances come from the Grid (upstream), or from the energy supplier since even the most advanced transmission and distribution systems are unable to guarantee the supply with absolute continuity and perfect quality – having a significant effect in the quality of the supplied voltage. In this sense, the complexity of the energy generation system like Renewable Energy Sources, and their growing diffusion, has certainly a significant impact on the quality of the voltage supplied.
Unawareness of risks and consequences
However, industries which are using automation systems, are largely unaware of the need to ensure the optimal Power Quality that automation puts at risk. There is a significant gap in knowledge about the problems and risks involved in the lack of good Power Quality in the production processes. Thus, people associated with the operation of machinery (Technical Managers, Production Managers, etc.) consider the purchase of equipment to ensure Power Quality as unnecessary and often as a luxury.
But in reality, the lack of Power Quality is one of the main causes of sudden and unplanned shutdowns of the production process, damage to equipment or in the electrical and mechanical infrastructure, resulting in simultaneous financial losses due to increased losses from factors such as harmonics and the low power factor (cosφ).
How to deal with the Power Quality issue
Dealing with the issue of Power Quality is always a difficult and complex issue. To deal effectively, a holistic approach to the issue is required, together with gathering sufficient data and information.
One or more measurements are required to collect the necessary data and information; in other words, a whole “campaign” of measurement on a case-by-case basis. In addition, the electrical structure of the plant facilities and production flow processes are required in order to clarify what is happening.
In the above issues, more than one person in charge is usually involved. For example, the specialist in electrical measurements (who is usually also the specialist in the electrical system), the specialist in Power Quality, and the plant managers (technical director and production manager). All of them are involved – more or less – in the above issues and should inevitably be involved in the problem-solving process. These people have the information and their role is catalytic, even in cases where the cause of the problem may not be known but only the results.
Below we will focus on measurements because as a topic it deserves a lot of analysis and is crucial in solving a Power Quality issue. It is, after all, the first step in the investigation process, and in case that it is misdirected from the beginning, it will lead with mathematical precision to a dead end.
Actions before measurements
Before the measurements begin, it will be necessary to have a full dialogue with those who are well acquainted with the production and operation processes of the industrial plant and what are the problems they are facing – what is happening, in which functions of the factory, what hours and days, at what time of year? Did the problems start before or after system changes? For example, before or after the addition of photovoltaic systems or the increase in production lines? Are the problems involving one machine or more? (Cooperation with the machine manufacturer may also be required to investigate the type of errors and possibly their causes).
Both manuals and design are also required to be checked. For example, the monogram design should be checked to see if it corresponds to reality or if it is too old. These documents help identify loads, the operation of which can cause problems for the rest of the equipment.
Before the measurements, an autopsy must also be performed on the installation. Significant information can be gathered under empirical perspective and judgment (machine status, short circuit cases, overload, overheating, presence of conductive dust pollution, etc.), by hearing (sounds from the inside of machines and their performance according to active loads) and by touch (temperature of covers or humidity). Of course, all these empirical tests should not override the safety rules.
Recording and understanding the energy provider’s bills for an entire year, as opposed to the production schedule, is also very important to get a more complete picture – especially in the case of units that do not operate continuously throughout the year.
In cases where there is a surveillance system with data recording, these should be taken into consideration after it is ensured that the measuring instruments in the field provide real data.
Strategy of Measurements
All of the above information, after being studied thoroughly, leads to the strategy of measurements or in other words, the way in which measurements should be made in order to lead to sufficient and valid results. Questions are being answered about where, when, and for how long the measurements should be made.
The measurement strategy is crucial. Measurements make no sense – no matter how detailed they are – without a very good knowledge of the general behavior and operation of the installation.
Before starting the measurements, the following questions should have been answered, so that there is a clear plan for complete and valid measurements.
Where should measurements be performed?
At what points in the system should the measurements be performed? Indicatively, on the terminals of the disturbed loads, on the terminals of the harmful loads, after the medium-voltage transformer, etc.
When should measurements be performed?
If you want to measure the maximum harmonic deformation of the current and voltage or the minimum voltage, then the measurements should be made at the full system load (or at the start of the main loads).
If you want to evaluate any voltage fluctuations in relation to the nominal value, measure in non-operating hours or in those hours with the minimum operation of the installation.
In case of problems, which are encountered during certain processes or situations of the system, it is self-evident that measurements should be made when reproducing these conditions as much as possible. Attention should be paid to facilities with seasonal operations, such as the processing of fruits and vegetables and those associated with photovoltaic systems.
How long should the measurements last?
Measurements aimed at identifying the total harmonic voltage (THDV) and current (THDI) index can last up to a few quarters of an hour, as long as – as mentioned above – they are performed when the system is at maximum load.
On the other hand, measurements that are oriented towards the voltage or behavior of electricity should be performed at least for a full week (EN 50160).
Statistical surveys (for example, measuring voltage drops and their duration and depth characteristics) require continuous measurement at least for a few months. It is even better to have the data available – from the power supplier – of the voltage drops (SAGs) of the previous year, in medium voltage.
After all, what needs to be clarified is what kind of measurements need to be made and what tools need to be used. This is something that is evaluated on a case-by-case basis. The ability and added value of knowledge from the experts in electrical measurements play a key role in answering these questions.
EMMIS provides complete Power Quality solutions to industries, marine, and large buildings.
It has a complete product portfolio and the right equipment to deal with disturbances and the optimization of power quality, such as active harmonic filters, voltage stabilizers, power factor correction systems, and power analyzers.
It approaches the problem of power quality holistically, ensuring the accuracy and validity of measurements. It proposes the appropriate equipment depending on the case and the results of the measurements and performs all the necessary actions for the installation, commissioning, and maintenance of the equipment.